Using the Right Grinding Wheel for the Welding Job
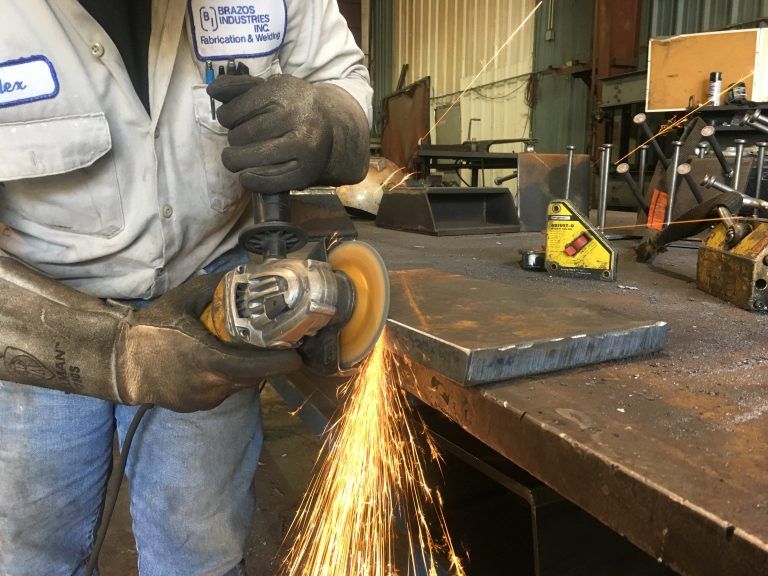
A good weld begins with good preparation, and good weld preparation begins with a clean cut. However, cutting is an art that requires both skill and knowledge of how to select and utilize the best grinding wheel for the job. The type of grinding wheel to use for a given application depends largely on what material you are cutting. We will discuss using the right grinding wheel for the welding job.
Grinding Wheel for the Welding Job
Abrasive—Grits and Grains
The most common abrasive in grinding wheels is aluminum oxide. Typically, it is the abrasive you use for grinding the following:
- carbon steel
- alloy steel
- high speed steel
- annealed malleable iron
- wrought iron
- bronzes and similar metals
Another family of abrasives is zirconia alumina. This aluminum oxide and zirconium oxide combination results in a tough, durable abrasive that works well in rough grinding applications.
Silicon carbide
is another common abrasive for grinding the following:
- gray iron
- chilled iron
- brass
- soft bronze
- aluminum
- stone
- rubber
- other non-ferrous materials
Once you know the grain, the next question relates to grit size. All grinding wheels contain a number designating this characteristic. It corresponds to the number of openings per linear inch in the final screen size utilized to size the grain.
Buying Bonds
Allowing the abrasive in the wheel to cut efficiently requires that the wheel to contain the proper bond. It must also wear away as the abrasive grains wear and expell so there’s exposure to new sharp grains.
There are three principle bond types in conventional grinding wheels. Each of which, is capable of giving distinct characteristics to the grinding action on the wheel. The type of bond chosen depends on such factors as the following:
- wheel operating speed
- the type of grinding operation
- the precision required
- the material you’re grinding
The majority of grinding wheels have vitrified bonds, consisting of a mixture of carefully selected clays. The clays and the abrasive grains fuse into a molten glass condition at the high temperatures produced in the kilns where grinding wheels are made. The glass forms a span that attaches each grain to its neighbor and supports the grains while they grind during cooling.
Some bonds consist of organic substances. They soften under the heat of grinding. Resinoid bond is the most common organic bond type. It consists of synthetic resin. Grinding wheels with resinoid bonds are ideal choices for applications that require rapid stock removal, as well as those where better finishes are necessary.
Rubber is another type of organic bond. Rubber bonds offer a smooth grinding action, and are common in wheels where a high quality of finish is necessary, such as ball bearing and roller bearing races. They are also common for cut-off wheels where you hold burr and burn to a minimum.
Wheel Shapes
The wheel comes in various shapes, the most common being the straight wheel. The grinding face is the part of the wheel that addresses the work. It is on the periphery of a straight wheel. A common variation of the straight wheel design is the recessed wheel.
Some wheels have the cutting face on the side of the wheel. These wheels are typically named for their distinctive shapes, as in cylinder wheels, cup wheels and dish wheels. Bonded abrasive sections of various shapes are sometimes assembled to form a continuous or intermittent side of grinding wheel. These products are called segments. Wheels with cutting faces on their sides common to grind the teeth of cutting tools and other hard-to-reach surfaces.
Mounted wheels are small grinding wheels with special shapes. These shapes include cones or plugs that are permanently mounted on a steel mandrel. The are common for various off-hand and precision internal grinding jobs.
Putting it All Together
You must consider numerous factors to select the best grinding wheel for the welding job. These factors include the following:
- Material you are grinding. This determines the kind of abrasive you will need in the wheel.
- The amount of stock you’re removing. Coarser grits provide rapid stock removal since they are capable of greater penetration and heavier cuts.
- Area of grinding contact between the wheel and the workplace. Use a wheel with coarser grit and softer grade for a broad area of contact to ensure a free, cool cutting action under the heavier load imposed by the size of the surface to be ground.
- The severity of the grinding action. This is the pressure under which the grinding wheel and the workpiece are brought and held together.
- Grinding machine horsepower. Generally, it’s necessary to use harder grade wheels on machines with higher horsepower.
These are just a few aspects to consider for selecting the right grinding wheel for the welding job. Contact Brazos Industries with the link below for more information on grinders!
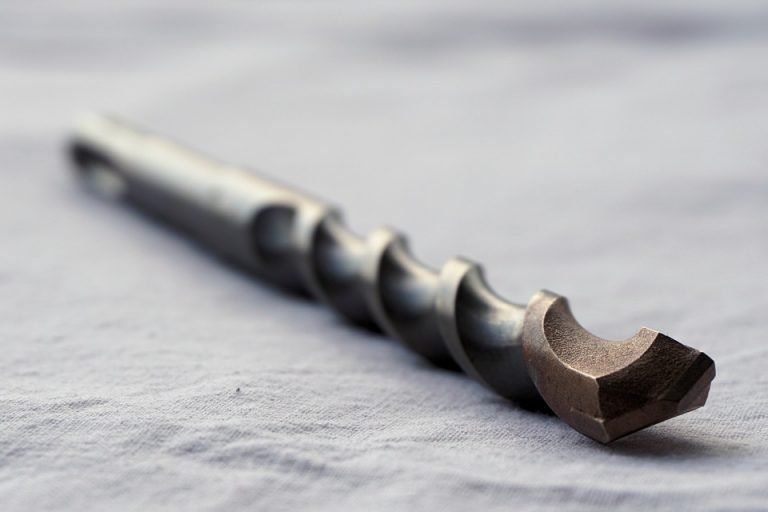
Many are unaware that drill bits require regular sharpening to give their best service. Similar to knives and axes, a dull drill bit requires much more force to do the same job. Instead of wearing the user out, a dull drill bit will inevitably wear out your drill. Giving your drill bits regular spot sharpening with a file is the best way to protect your investment in high-quality power tools. Brazos Industries knows the importance of properly sharpening drill bits, and we would like to share with you how to sharpen drill bits to protect your investment.
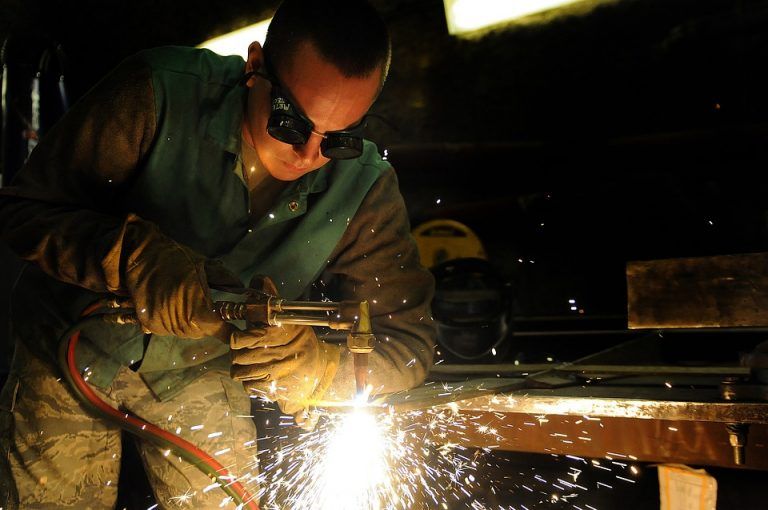
Eye injuries account for one-quarter of all welding injuries. This makes them by far the most common injury for welders, according to research from the Liberty Mutual Research Institute for Safety. Those most at risk for welding-related eye injuries are workers in industries that produce industrial and commercial machinery, computer equipment and fabricated metal products. Therefore, we will discuss the importance of safety glasses for welding.
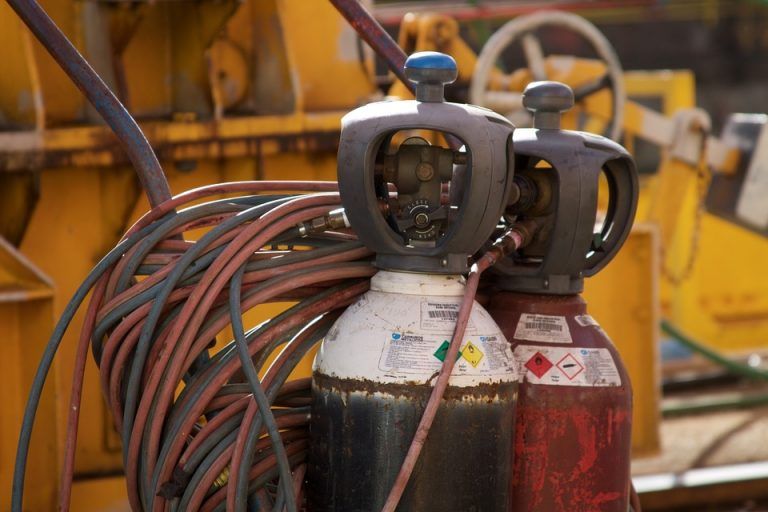
Following a regiment of appropriate and thorough maintenance procedures allows a welding machine to run safely and dependably for a long time. Improper, incomplete or totally neglected maintenance can not only result in equipment failure, but it can also lead to serious hazards including severe injury or even death. With some forethought and basic planning, welding machine maintenance is extremely easy.
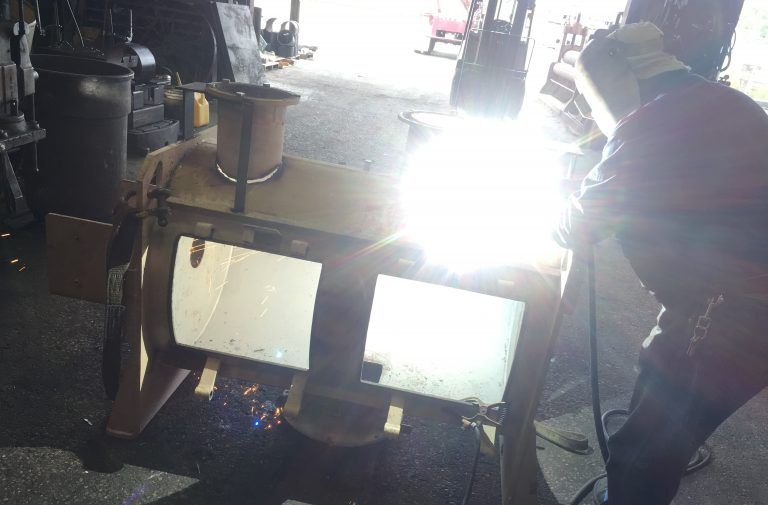
Air arc gouging is a process of removing metal by using heat generated from a carbon arc. This process utilizes a carbon/graphite electrode, compressed air and a standard power source. The extreme heat arc created between the electrode and a metal workpiece gouges and melts the workpiece. The compressed air also blows away the molten metal. This process is common for cutting stainless steel, carbon steel and alloys of copper, brass, aluminum and magnesium.
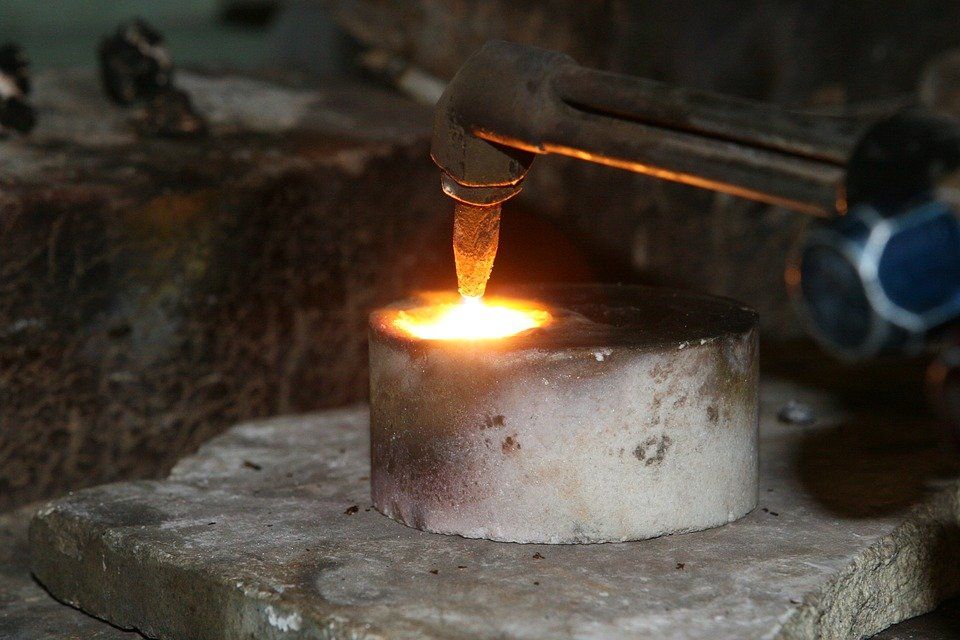
You can fit oxy-fuel torches with a “Cutting Head” and use them to cut one solid piece of metal into two or more pieces. Lighting, adjusting and shutting down an oxygen-acetylene torch is easy, particularly when following to proper procedures. We will discuss properly adjusting the flames for the oxy-fuel cutting.
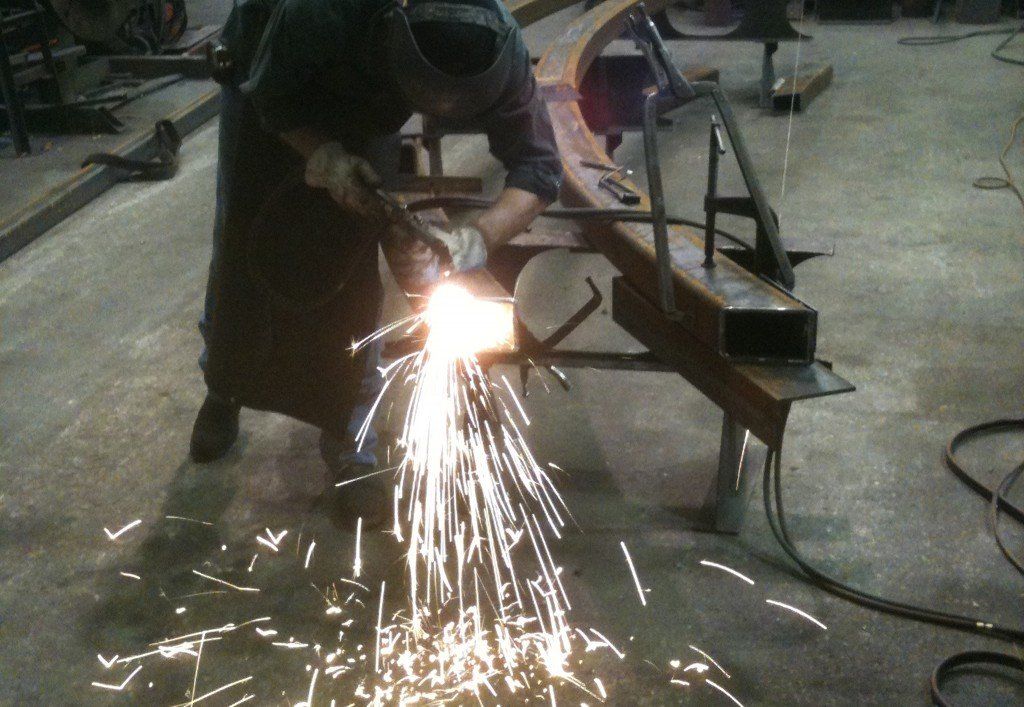
Selecting the right cutting or styling tool for the job means the difference between an average cut or a great cut. Therefore, it is important to choose carefully. It is critical to both performance and safety to choose the correct tip for the job. Here’s a simple step-by-step process for choosing the right cutting tip to ensure you deliver a great cut every time.