The Importance of Welding Machine Maintenance
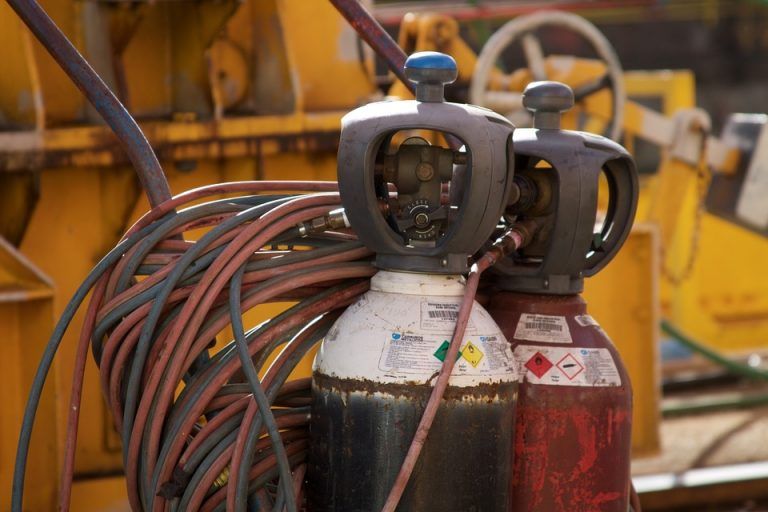
Following a regiment of appropriate and thorough maintenance procedures allows a welding machine to run safely and dependably for a long time. Improper, incomplete or totally neglected maintenance can not only result in equipment failure, but it can also lead to serious hazards including severe injury or even death. With some forethought and basic planning, welding machine maintenance is extremely easy.
Welding Machine Maintenance
Electrical Systems
Electricity plays a significant role in welding, as it is the primary power source for most welding processes, oxy-acetylene gas welding being the only exception. The dangers of electricity are huge, and the consequences of accidents resulting from problems with electricity include debilitating injury or death. These risks necessitate regular inspection of all electrical components incorporated in your welding machine. This includes the following routine practices:
- Disconnect all of the power units and blow out or vacuum the machines interior at least once every six months.
- Check and clean (with a wire brush) the wire feeder and drive rolls (replacing if necessary) at least once every three to four months. In addition, inspect and cleaning (or replacing if necessary) the inlet and outlet guides.
- Arrange for a technician to service the welding gun and liner assembly at least once a year.
- Inspect all of the electrical cables at least once a month for signs of wear, including cracks and breaks, immediately replacing any cables with excessively worn or damaged insulation.
- Inspect electrical safety equipment on a monthly basis to ensure circuit breaks and interlocks are functioning properly.
Shielding Gas Cylinder Maintenance
Always store shielding gas cylinders in a cool and dry environment. Also, make sure to keep them in an upright position. Inspect and test regulators and valves at least once every six months to make sure there are no leaks or breaches that are causing incorrect pressure readings.
The hoses need to be coiled up for storage. This will prevent damage from prolonged kinks that occurs when hoses are improperly stored or stepped on when left on the ground. Any creaked or damaged hoses require replacement immediately.
Routine Maintenance Schedule
The following are routine maintenance schedules by the hours:
8 Hours Maintenance
- Wipe up oil and fuel spills right away
- Check the fluid levels (oil and fuel)
- Service the air filter
50 Hours Maintenance
- Service the air filter element
- Clean and tighten the weld terminals
100 Hours Maintenance
- Chang the oil
- Change the oil filter
- Change and tighten the battery connections
- Clean the cooling system
200 Hours Maintenance
- Replace the unreadable labels
- Replace the fuel filter
- Check the valve clearance
250 Hours Maintenance
- Check and clean the spark arrestor
500 Hours Maintenance
- Tape or replace cracked cables
- Clean/set injectors
1000 Hours Maintenance
Blow out or vacuum the inside of the equipment. Make sure to do this monthly during heavy service.
Creating and staying on top of a regular welding machine maintenance schedule allows you to not only ensure your equipment works when you need it most and lasts for many years to come, but also operates at peak performance, guaranteeing your safety. Don’t hesitate to contact us here at Brazos Industries with the link below for more information!
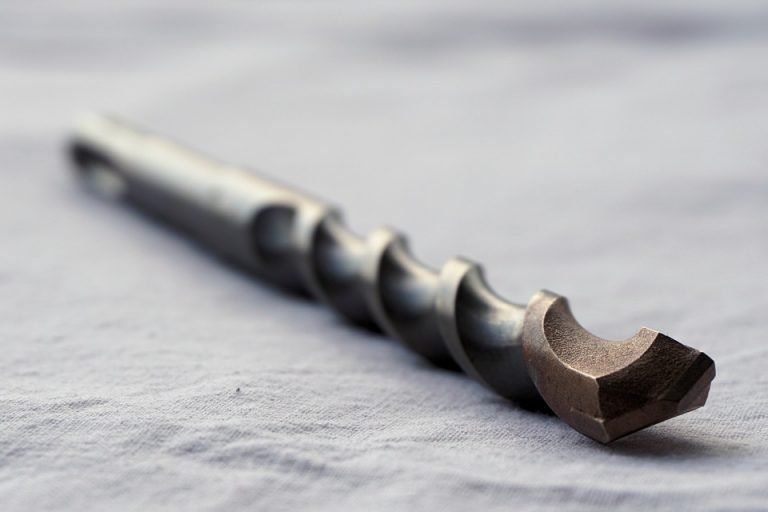
Many are unaware that drill bits require regular sharpening to give their best service. Similar to knives and axes, a dull drill bit requires much more force to do the same job. Instead of wearing the user out, a dull drill bit will inevitably wear out your drill. Giving your drill bits regular spot sharpening with a file is the best way to protect your investment in high-quality power tools. Brazos Industries knows the importance of properly sharpening drill bits, and we would like to share with you how to sharpen drill bits to protect your investment.
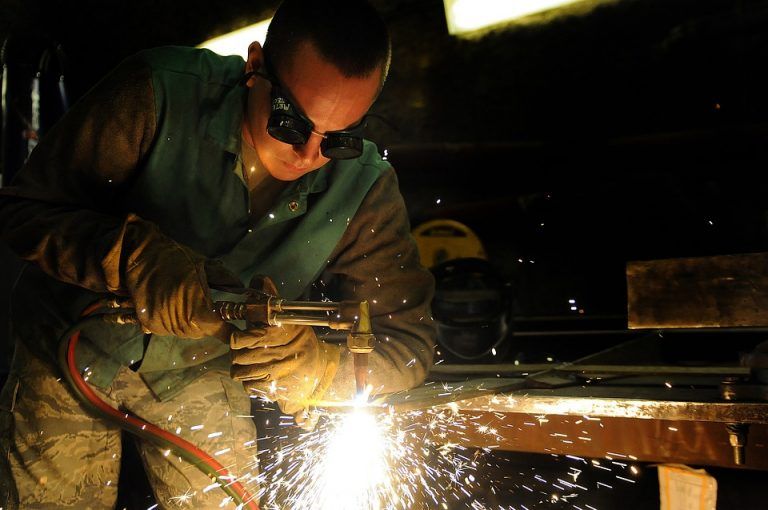
Eye injuries account for one-quarter of all welding injuries. This makes them by far the most common injury for welders, according to research from the Liberty Mutual Research Institute for Safety. Those most at risk for welding-related eye injuries are workers in industries that produce industrial and commercial machinery, computer equipment and fabricated metal products. Therefore, we will discuss the importance of safety glasses for welding.
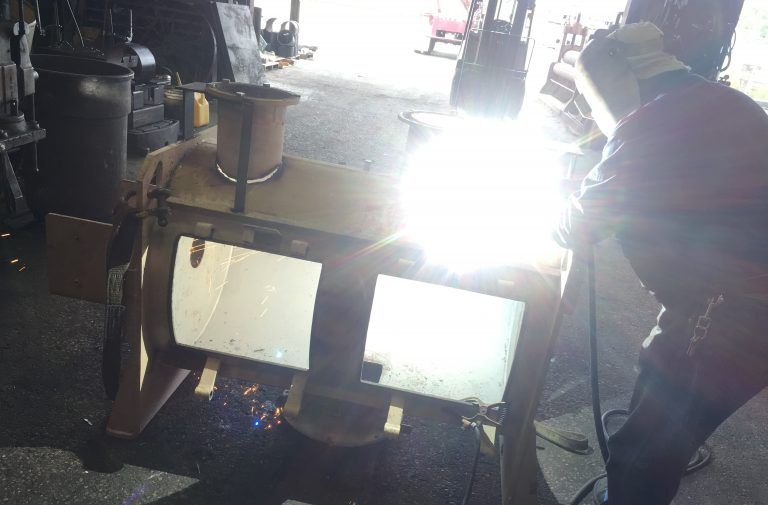
Air arc gouging is a process of removing metal by using heat generated from a carbon arc. This process utilizes a carbon/graphite electrode, compressed air and a standard power source. The extreme heat arc created between the electrode and a metal workpiece gouges and melts the workpiece. The compressed air also blows away the molten metal. This process is common for cutting stainless steel, carbon steel and alloys of copper, brass, aluminum and magnesium.

A good weld begins with good preparation, and good weld preparation begins with a clean cut. However, cutting is an art that requires both skill and knowledge of how to select and utilize the best grinding wheel for the job. The type of grinding wheel to use for a given application depends largely on what material you are cutting. We will discuss using the right grinding wheel for the welding job.
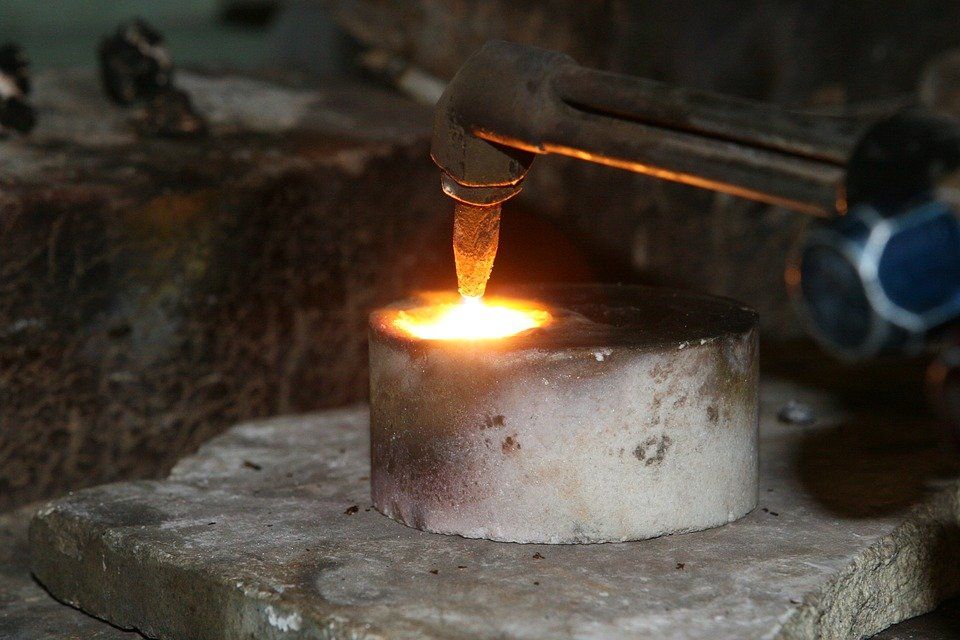
You can fit oxy-fuel torches with a “Cutting Head” and use them to cut one solid piece of metal into two or more pieces. Lighting, adjusting and shutting down an oxygen-acetylene torch is easy, particularly when following to proper procedures. We will discuss properly adjusting the flames for the oxy-fuel cutting.
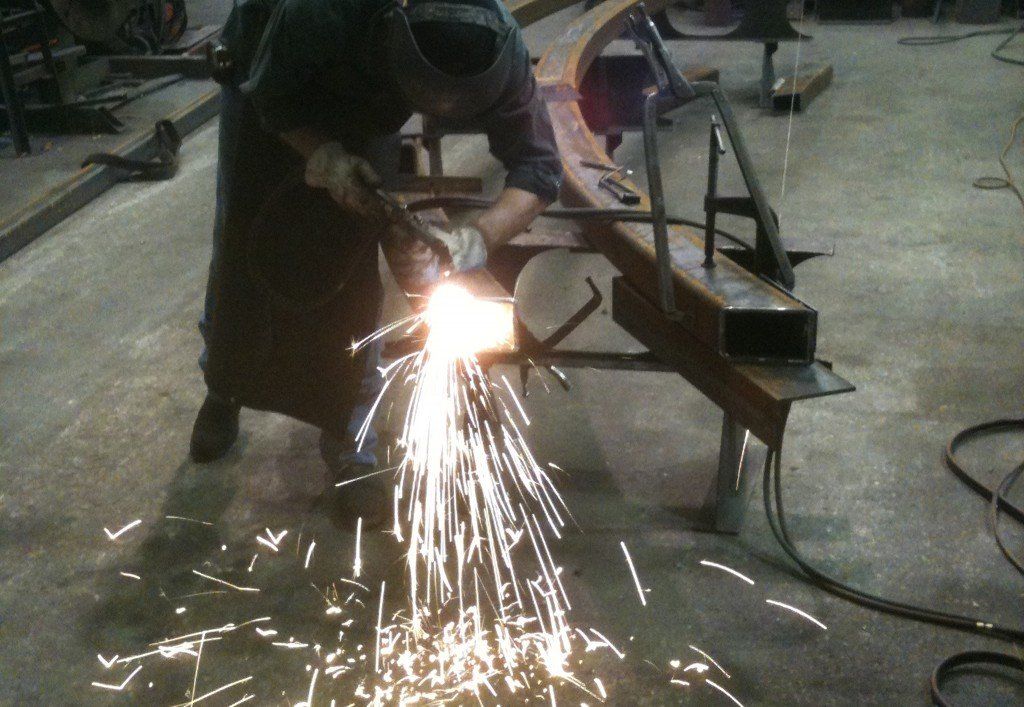
Selecting the right cutting or styling tool for the job means the difference between an average cut or a great cut. Therefore, it is important to choose carefully. It is critical to both performance and safety to choose the correct tip for the job. Here’s a simple step-by-step process for choosing the right cutting tip to ensure you deliver a great cut every time.