How to Sharpen Drill Bits to Protect Your Investment in High-Quality Power Tools
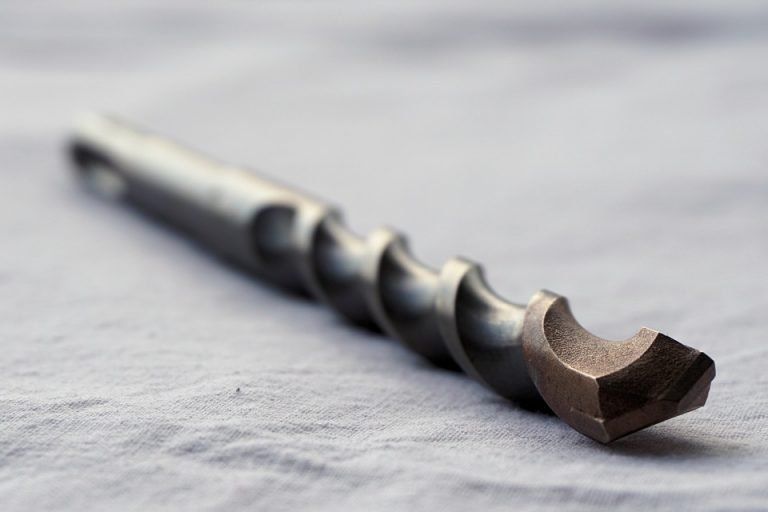
Many are unaware that drill bits require regular sharpening to give their best service. Similar to knives and axes, a dull drill bit requires much more force to do the same job. Instead of wearing the user out, a dull drill bit will inevitably wear out your drill. Giving your drill bits regular spot sharpening with a file is the best way to protect your investment in high-quality power tools. Brazos Industries knows the importance of properly sharpening drill bits, and we would like to share with you how to sharpen drill bits to protect your investment.
How to Sharpen Drill Bits Safely
Preparing to Sharpening Drill Bits
Before beginning, Brazos Industries makes sure to follow safety precautions, as sharpening a drill bit will cause metal to fly through the air. Our team also wears eye protection to further prevent injury and mistakes from occurring. Leather gloves will also assist in protecting your hands.
When necessary, our team here at Brazos Industries uses a vise or a sharpening jig to hold the drill bit. Use a pair pliers if you don’t have access to this. It is ideal to keep your hands away from the grinder.
Sharpening Drill Bits to Prevent Overheating
Correctly sharpening the drill bit requires the grinder to be at a slow speed. Placing he bit against the base of the wheel allows the sloped side to touch the cutter. This should be near a 60-degree angle for most bits. The tip of the bit should not touch grinder.
Brazos Industries slowly rotates the bit in a clockwise motion, while removing and placing it in a glass of water every few seconds. This will prevent the bit from overheating.
Testing the Drill Helps Prevent Mistakes
Every so often our welders will check the sharpness of the drill bit. Simply touching the drill bit with your finger can achieve this. If it is sharp then you won’t need to continue using the grinder. Also, you will need to examine the angle of the drill bit.
Brazos Industries suggests utilizing a protractor to ensure that the bit still has a 60-degree angle. Periodically checking this throughout the process will prevent any mistakes.
Methodically Using a Metal File for Sharpening Drill Bits to Prevent Any Accidents
Once the drill bit is fairly sharp, you will need to use a metal file to finish the job, as this will prevent over-sharpening of the bit. Put the bit in a vise or clamp and utilize a metal file to sharpen it. Keep the file at an angle. To prevent any mistakes, make sure to do this slowly and methodically.
Maintaining the Drill Bit Regularly is Crucial Here at Brazos Industries
Brazos Industries maintains our drill bits regularly to avoid the possible mistakes and accidents from occurring. While we perform maintenance frequently, this prevents our drill bits from becoming too dull to use.
Additionally, we store our drill bits are correctly in the original casing to reduce the chances of an accident occurring.
These are just the basics how to sharpen drill bits. Don’t hesitate to contact us with the link below for more information!
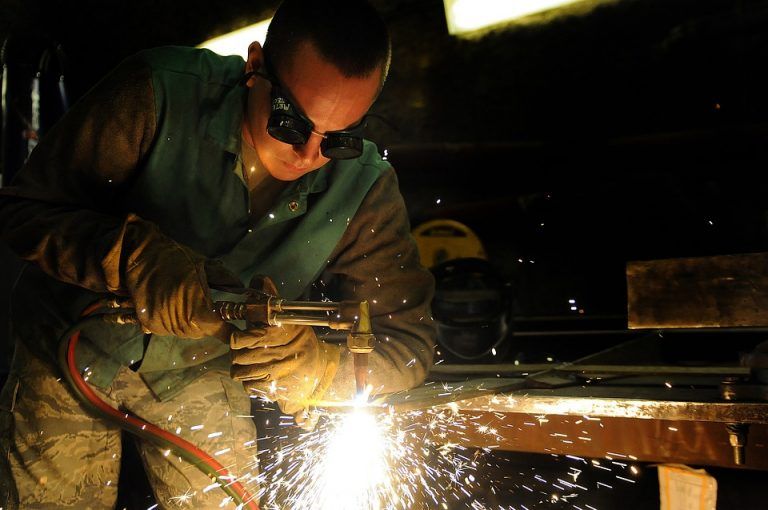
Eye injuries account for one-quarter of all welding injuries. This makes them by far the most common injury for welders, according to research from the Liberty Mutual Research Institute for Safety. Those most at risk for welding-related eye injuries are workers in industries that produce industrial and commercial machinery, computer equipment and fabricated metal products. Therefore, we will discuss the importance of safety glasses for welding.
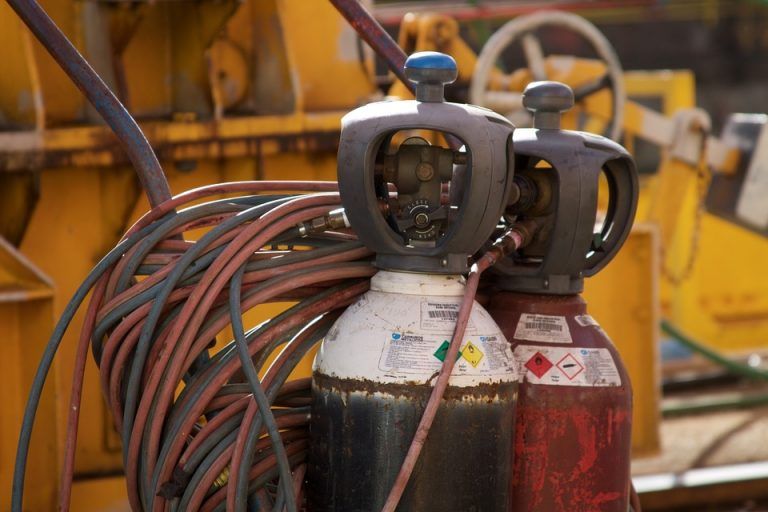
Following a regiment of appropriate and thorough maintenance procedures allows a welding machine to run safely and dependably for a long time. Improper, incomplete or totally neglected maintenance can not only result in equipment failure, but it can also lead to serious hazards including severe injury or even death. With some forethought and basic planning, welding machine maintenance is extremely easy.
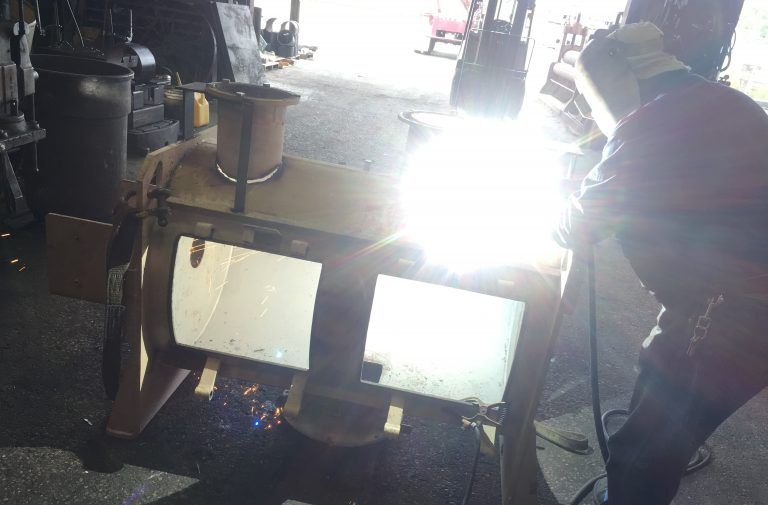
Air arc gouging is a process of removing metal by using heat generated from a carbon arc. This process utilizes a carbon/graphite electrode, compressed air and a standard power source. The extreme heat arc created between the electrode and a metal workpiece gouges and melts the workpiece. The compressed air also blows away the molten metal. This process is common for cutting stainless steel, carbon steel and alloys of copper, brass, aluminum and magnesium.

A good weld begins with good preparation, and good weld preparation begins with a clean cut. However, cutting is an art that requires both skill and knowledge of how to select and utilize the best grinding wheel for the job. The type of grinding wheel to use for a given application depends largely on what material you are cutting. We will discuss using the right grinding wheel for the welding job.
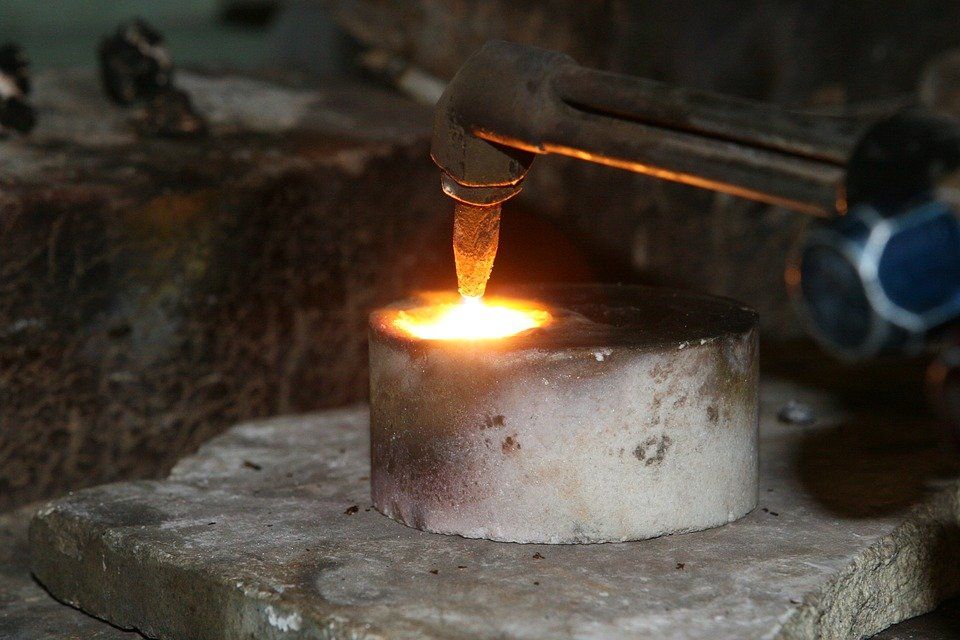
You can fit oxy-fuel torches with a “Cutting Head” and use them to cut one solid piece of metal into two or more pieces. Lighting, adjusting and shutting down an oxygen-acetylene torch is easy, particularly when following to proper procedures. We will discuss properly adjusting the flames for the oxy-fuel cutting.
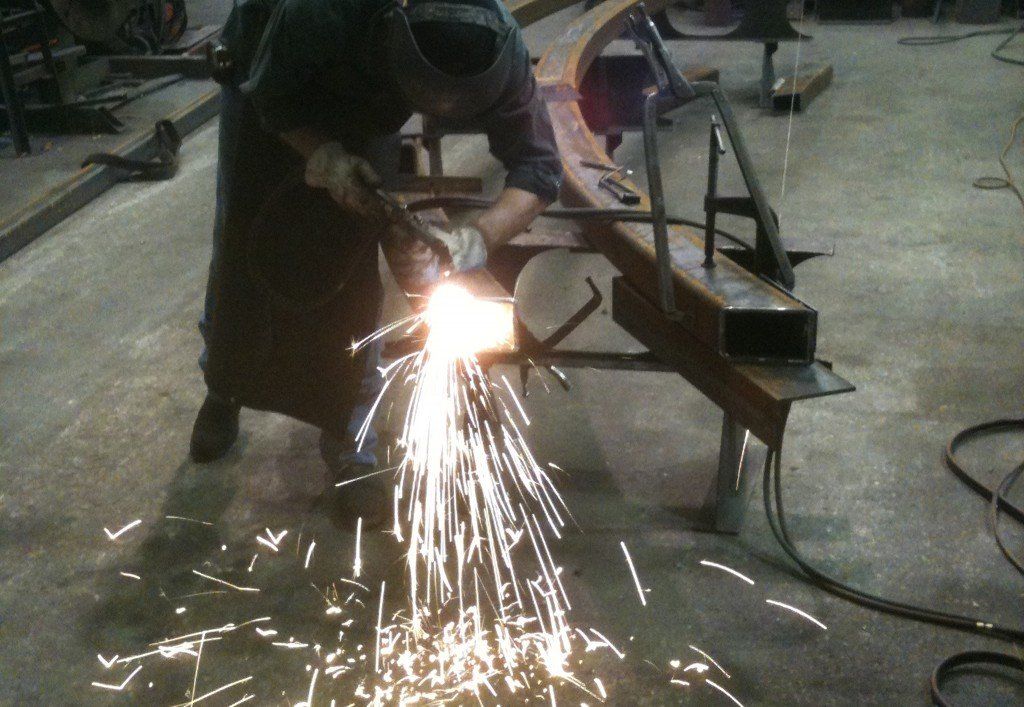
Selecting the right cutting or styling tool for the job means the difference between an average cut or a great cut. Therefore, it is important to choose carefully. It is critical to both performance and safety to choose the correct tip for the job. Here’s a simple step-by-step process for choosing the right cutting tip to ensure you deliver a great cut every time.