Properly Adjusting the Flames for the Oxy-Fuel Cutting
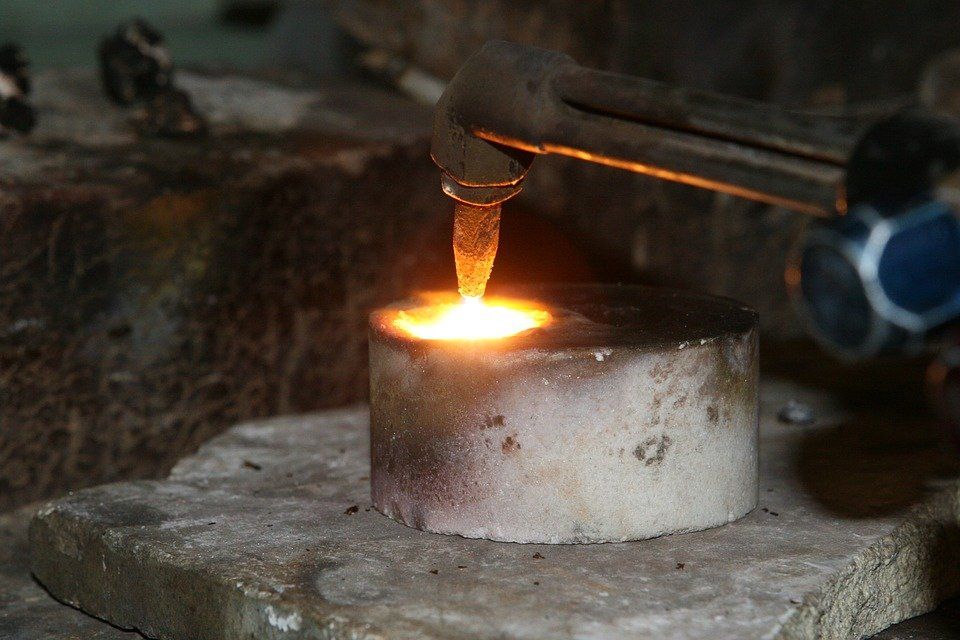
You can fit oxy-fuel torches with a “Cutting Head” and use them to cut one solid piece of metal into two or more pieces. Lighting, adjusting and shutting down an oxygen-acetylene torch is easy, particularly when following to proper procedures. We will discuss properly adjusting the flames for the oxy-fuel cutting.
Adjusting the Flames for the Oxy-Fuel Cutting
Preheat
Flame cutting/oxygen cutting requires some source of intense of heat to get the plate hot enough to cut/burn. This source of heat is referred to as the “preheat flame”. Therefore, it’s only necessary to heat the portion slightly ahead of the cutting reaction, not the entire plate.
There are a few plate materials that require “preheating” before cutting to keep them from cracking during cutting. Generally, materials with carbon levels above .25% fall in this category. However, this is not the “preheat” we are referring to.
Preheat Gases
A number of fuels are common for the oxy-fuel mixture called Preheat. Also, each has some feature to make it attractive.
Up until about 1970 Acetylene was the primary fuel of use. However, its escalating costs, the growth of plasma and the aggressive marketing of other fuels which has resulted in it no longer being a primary choice especially where plasma is also available.
Flame Temperature
A high heat transfer rate from the flame to the plate is necessary. The aspects the operator can control to achieve the transfer of heat include:
- flame temperature
- quantity of preheat gases used
- tip to work distance
Adjusting the O/F Ration allows for the control of the flame temperature. Raising or lowering the preheat pressures to the torch allows for adjustments of the quantity of preheat. High pressure results in high flowrates, i.e. a high velocity preheat. Low pressures result in low flowrates/velocity. The operator can adjust the O/F ratio by looking at the inner cone of the flame.
In addition, the quantity of preheat necessary varies depending on the operation you are conducting. For a pierce start, a very high flowrate (at the right O/F ratio) is necessary followed by an increasingly lower flowrate (at the right O/F ratio) for the continuing cutting operation. These preheat conditions are Hi Preheat and Lo Preheat. Pierce time is the time the Hi Preheat is on prior to initiation of the cutting oxygen.
Preheat Problems
Properly adjusting a preheat setting will result in a sharp top edge and a slag free and sharp bottom edge. The mill scale is extremely heavy. In this case, a higher preheat will sometimes be necessary to break the mill scale loose while keeping the leading edge of the cut properly heated.
Too much preheat can cause a rounded top edge as well as a significant increase in slag. This increase in slag frequently results in a cut that will not drop from the base plate. The slag is sometimes so tenacious that the part must be beat out of the plate with a sledge hammer.
Preheat Quantities
The actual recommended quantity (CFH) of oxy-fuel varies with the tip manufacturer and tip purpose.
For practical shape cutting, the quantities typically required are Natural Gas 10-20 CFH and 18- CFH Oxygen and Propane 5-10 CFH and 23-45CFH Oxygen.
These are just the basics of properly adjusting the flames for the oxy-fuel cutting. Brazos Industries continually adds capabilities of new machinery to satisfy growing customer needs. We carry a wide array of steel products for any of your current or future project needs. Contact us with the link below to purchase any of our products in inventory!
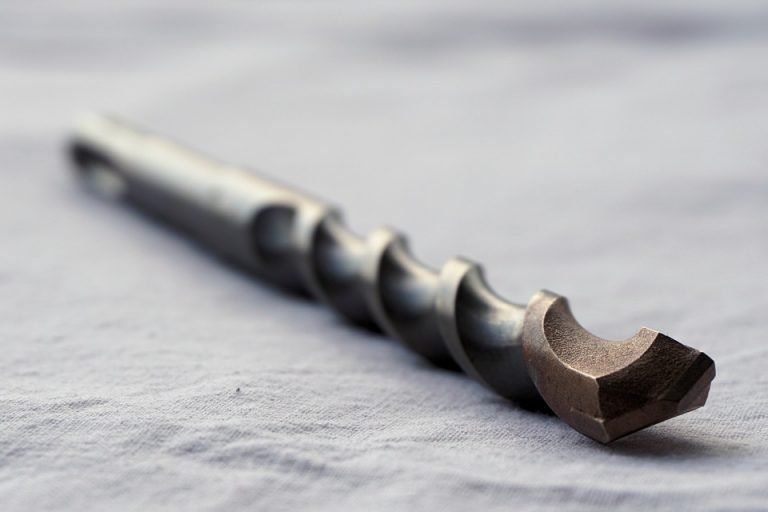
Many are unaware that drill bits require regular sharpening to give their best service. Similar to knives and axes, a dull drill bit requires much more force to do the same job. Instead of wearing the user out, a dull drill bit will inevitably wear out your drill. Giving your drill bits regular spot sharpening with a file is the best way to protect your investment in high-quality power tools. Brazos Industries knows the importance of properly sharpening drill bits, and we would like to share with you how to sharpen drill bits to protect your investment.
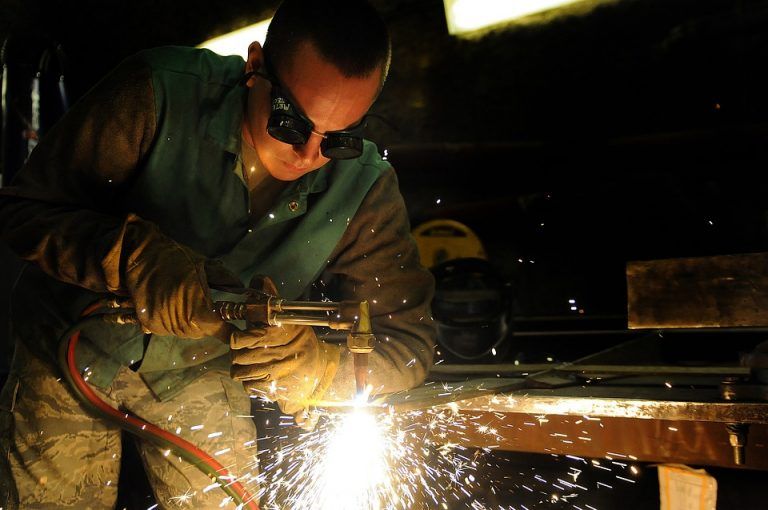
Eye injuries account for one-quarter of all welding injuries. This makes them by far the most common injury for welders, according to research from the Liberty Mutual Research Institute for Safety. Those most at risk for welding-related eye injuries are workers in industries that produce industrial and commercial machinery, computer equipment and fabricated metal products. Therefore, we will discuss the importance of safety glasses for welding.
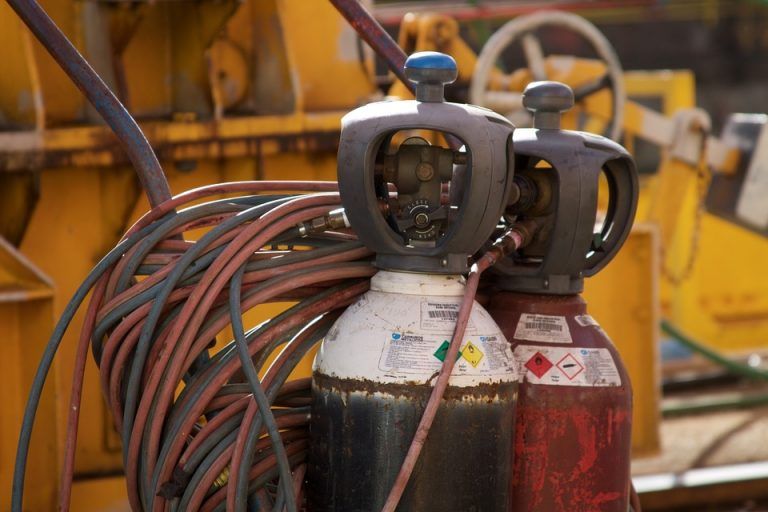
Following a regiment of appropriate and thorough maintenance procedures allows a welding machine to run safely and dependably for a long time. Improper, incomplete or totally neglected maintenance can not only result in equipment failure, but it can also lead to serious hazards including severe injury or even death. With some forethought and basic planning, welding machine maintenance is extremely easy.
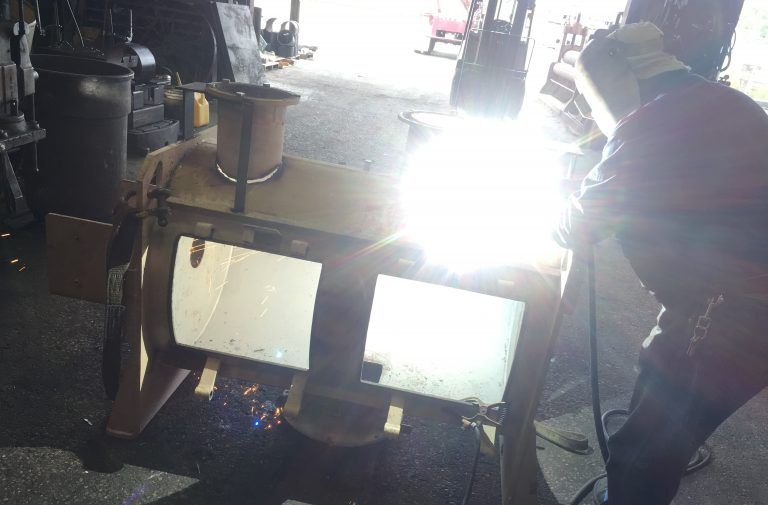
Air arc gouging is a process of removing metal by using heat generated from a carbon arc. This process utilizes a carbon/graphite electrode, compressed air and a standard power source. The extreme heat arc created between the electrode and a metal workpiece gouges and melts the workpiece. The compressed air also blows away the molten metal. This process is common for cutting stainless steel, carbon steel and alloys of copper, brass, aluminum and magnesium.

A good weld begins with good preparation, and good weld preparation begins with a clean cut. However, cutting is an art that requires both skill and knowledge of how to select and utilize the best grinding wheel for the job. The type of grinding wheel to use for a given application depends largely on what material you are cutting. We will discuss using the right grinding wheel for the welding job.
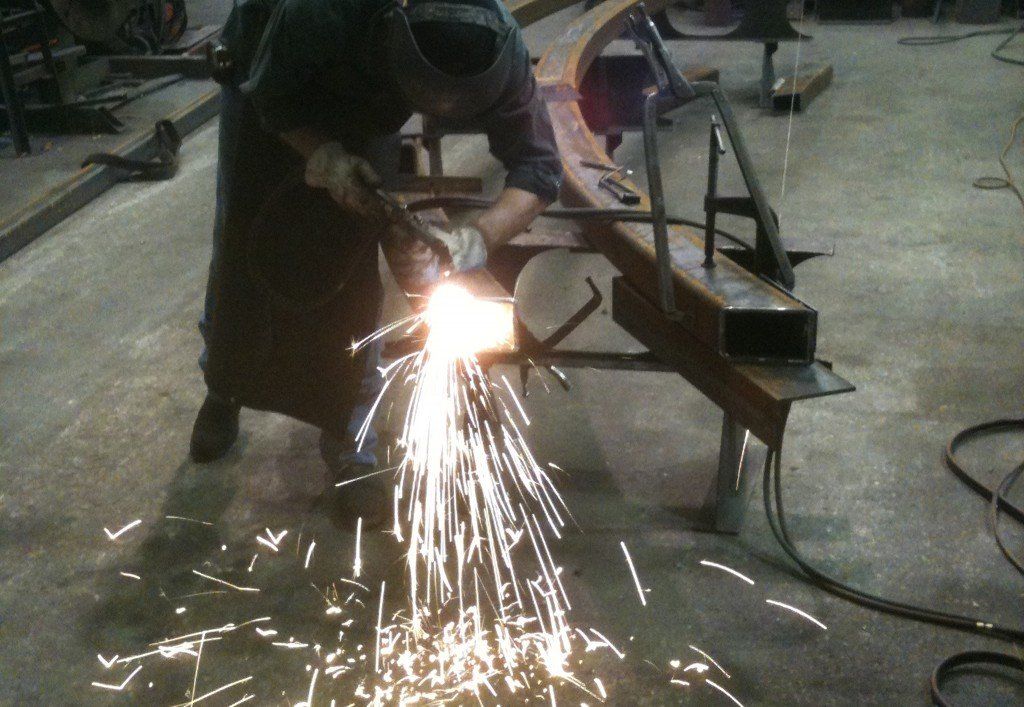
Selecting the right cutting or styling tool for the job means the difference between an average cut or a great cut. Therefore, it is important to choose carefully. It is critical to both performance and safety to choose the correct tip for the job. Here’s a simple step-by-step process for choosing the right cutting tip to ensure you deliver a great cut every time.